The world of metallurgy is vast and complex, encompassing a wide range of processes that allow us to create materials with specific properties tailored to various applications. Among these materials, the in999 alloys stand out due to their unique characteristics that make them suitable for numerous industrial uses, including electrical connectors, automotive parts, and decorative items. This article delves into the metallurgical processes involved in producing in 999 alloys, exploring the methods, advantages, and challenges associated with these high-performance materials.
Understanding in999 Alloys

What are in999 Alloys?
in999 alloys primarily refer to high-purity copper alloys characterized by their minimum copper content of 99.9%. This classification includes various grades of copper alloys with additional elements like tin, lead, or zinc, which enhance their physical and mechanical properties. These alloys are often used in applications requiring excellent thermal and electrical conductivity, corrosion resistance, and malleability.
Properties of in999 Alloys
The primary property that makes in999 alloys desirable is their exceptional conductivity. With minimal impurities, these alloys deliver superior performance in electrical applications. In addition to conductivity, they exhibit good tensile strength and ductility, allowing them to be easily formed and shaped without fracturing. The corrosion resistance of in999 alloys is also notable, making them ideal for use in harsh environments where exposure to moisture or chemicals could compromise other materials.
Application Areas of in999 Alloys
in999 alloys find extensive use across various industries. Electrical engineering relies heavily on these materials for wiring, connectors, and circuit boards. In the automotive sector, in999 alloys contribute to components where lightweight materials are essential for fuel efficiency. Additionally, the decorative arts utilize these alloys for jewelry and art pieces that benefit from their aesthetic appeal and high durability.
See more: in 999 register
Metallurgical Techniques for Producing in999 Alloys
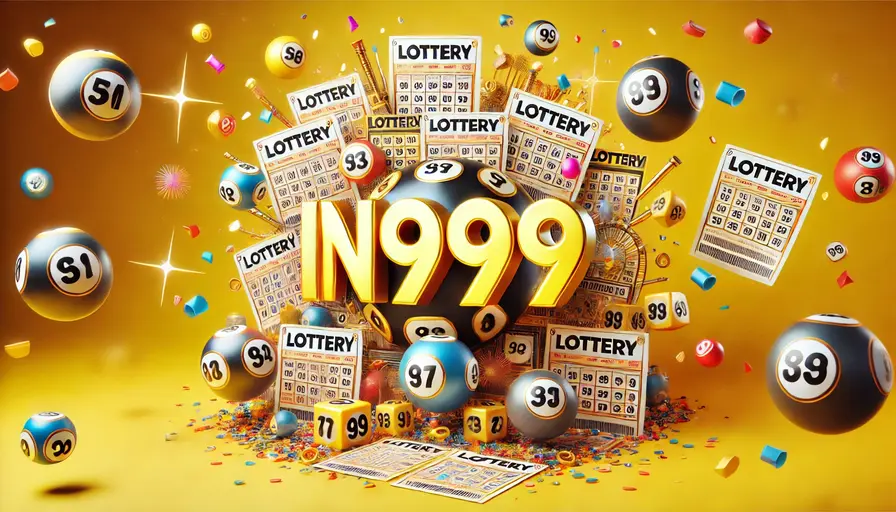
Melting and Casting Methods
Melting and casting are foundational processes in metallurgy that set the stage for alloy production. When creating in999 alloys, the melting process begins with carefully selected raw materials, typically high-purity copper and alloying elements.
Induction Melting
Induction melting is a popular method used to achieve high temperatures quickly and efficiently. Utilizing electromagnetic induction, this technique minimizes contamination risks while ensuring a uniform melt. This is crucial for achieving the purity standards required for in999 alloys. Once melted, the molten metal can be poured into molds to form ingots or other shapes, laying the groundwork for further processing.
Continuous Casting
Continuous casting is another effective method employed in the production of in999 alloys. In this technique, molten metal is poured into a cooled mold that allows it to solidify as it is continuously withdrawn. This process promotes a refined microstructure and consistent material properties, essential for applications demanding high reliability.
Alloying Process
Once the base materials are melted and cast into the desired shapes, the alloying process begins. This step involves adding specific elements to achieve the desired properties of the in999 alloy.
Element Selection
Selecting the right alloying elements is critical to the performance of in999 alloys. Commonly utilized elements include tin, which improves corrosion resistance and enhances strength. Lead may also be added to enhance machinability, especially in applications where precise shaping is necessary. Careful control of these additions ensures that the final product meets the rigorous standards expected of in999 alloys.
Homogenization Treatment
Following alloying, the homogenization treatment is often employed to eliminate compositional segregation and improve uniformity. This heat treatment process allows the alloy to reach a specific temperature, held for a predetermined time, before cooling. As a result, the internal structure becomes more homogeneous, optimizing both the mechanical and physical properties of the in999 alloy.
Advanced Processing Techniques for in999 Alloys
Cold Working
Cold working refers to the plastic deformation of metals at room temperature, leading to significant changes in their properties. For in999 alloys, this technique is pivotal in enhancing mechanical strength while maintaining formability.
Mechanisms of Strengthening
Through cold working, dislocations within the crystal lattice of the alloy increase, resulting in hindered motion of these dislocations under applied stress. This mechanism contributes to work hardening, improving strength and hardness. However, excessive cold working can lead to brittleness. Thus, careful monitoring is essential during processing.
Fabrication Techniques
Various fabrication techniques can be employed during the cold working phase. Techniques such as rolling, drawing, and extrusion are commonly used to shape in999 alloys into wires, sheets, and rods. Each method has distinct advantages, allowing manufacturers to tailor products to different specifications and applications.
Heat Treatment
Heat treatment is an integral part of the processing of in999 alloys, providing opportunities to optimize their properties further. Various heat treatment cycles can modify the structure and enhance the performance of the material.
Annealing Processes
Annealing is a common heat treatment performed on in999 alloys after cold working. This process involves heating the alloy to a specific temperature to relieve internal stresses and improve ductility. The annealed material can then undergo further processing or be used directly in applications requiring enhanced flexibility.
Age Hardening
Age hardening is another heat treatment process that can be applied to in999 alloys containing specific alloying elements. By heating and subsequently cooling the alloy, a fine distribution of precipitates forms within the matrix, enhancing hardness and strength. This technique is particularly beneficial in applications where durability is paramount.
Quality Control and Testing of in999 Alloys
Importance of Quality Assurance
In the production of in999 alloys, stringent quality assurance practices are vital to ensure that the final product meets industry standards. Quality control processes help detect potential defects, monitor material properties, and confirm compliance with regulatory requirements.
Inspection Techniques
Various inspection techniques are employed in the evaluation of in999 alloys. Non-destructive testing methods, such as ultrasonic testing and X-ray examination, enable manufacturers to identify internal defects without damaging the material. While visual inspections assess surface integrity and appearance, chemical analysis techniques verify alloy composition, confirming the purity levels essential for in999 alloys.
Mechanical Testing
Mechanical testing is critical for determining the performance characteristics of in999 alloys. Standard tests include tensile strength, hardness, and fatigue testing. These assessments provide valuable insights into how the material will perform under real-world conditions, aiding manufacturers in selecting the appropriate alloy for specific applications.
Standards and Certifications
Compliance with industry standards and certifications is paramount in the production of in999 alloys. Various organizations set guidelines for material properties, testing methods, and safety considerations.
International Standards
Organizations such as ASTM International, ISO, and SAE International offer standardized specifications for in999 alloys. Adhering to these standards not only ensures product quality but also facilitates international trade, allowing producers to meet the expectations of customers worldwide.
Certification Processes
Obtaining certifications for in999 alloys involves thorough audits and testing protocols. Manufacturers must demonstrate adherence to quality management systems, traceability, and continuous improvement practices. Achieving these certifications serves as a testament to the producer’s commitment to delivering high-quality materials.
FAQs
What is the difference between in999 alloys and standard copper alloys?
in999 alloys contain a minimum of 99.9% copper, while standard copper alloys may possess lower copper content and varying percentages of alloying elements. The high purity of in999 alloys results in superior conductivity and corrosion resistance compared to lower-grade materials.
Are in999 alloys suitable for outdoor applications?
Yes, in999 alloys exhibit excellent corrosion resistance, making them suitable for outdoor applications. However, proper surface treatment may still be recommended for extended exposure to harsh environmental conditions.
How does cold working affect the properties of in999 alloys?
Cold working enhances the mechanical strength of in999 alloys through work hardening mechanisms. However, excessive cold working can lead to reduced ductility and increased brittleness, necessitating careful control during processing.
Can in999 alloys be recycled?
Yes, in999 alloys can be recycled without significant loss of properties. Recycling helps conserve resources and reduces environmental impact, making it an attractive option for manufacturers seeking sustainable production practices.
What industries utilize in999 alloys most frequently?
in999 alloys find applications in various industries, including electrical engineering, automotive manufacturing, and decorative arts. Their high conductivity, corrosion resistance, and versatility make them invaluable in many sectors.
Conclusion
Metallurgical processes for producing in999 alloys encompass a variety of techniques, from melting and casting to advanced processing methods that enhance performance. With their exceptional properties and versatile applications, in999 alloys have become indispensable in modern manufacturing. Understanding these metallurgical processes not only highlights the complexity of alloy production but also underscores the importance of quality control and compliance in delivering high-performance materials. As industries continue to evolve, the demand for in999 alloys is likely to grow, driving advancements in metallurgical practices and fostering innovation in material science.